Genesis®
Structural Design Optimization Software
Genesis® Structural Analysis and Optimization Software
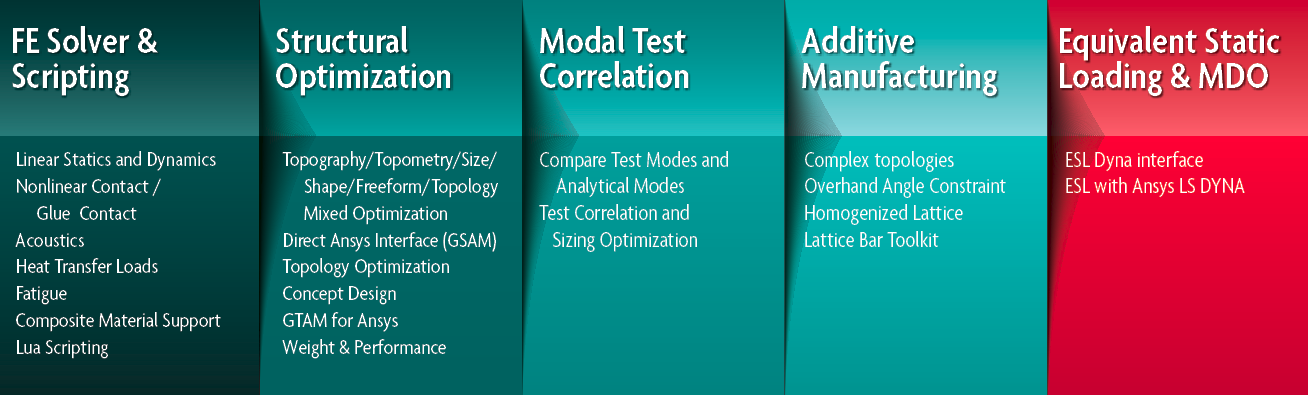
Analysis Includes:
- Statics
- Normal Modes
- System Buckling
- Heat Transfer
- Direct and Modal Frequency Analysis
- Random Response
Optimization Includes:
- Topology
- Sizing
- Shape
- Topometry
- Topography
- Freeform
What is it?
Genesis® is a Structural Analysis and Optimization Software that fully integrates analysis and optimization and it is written by leading experts in structural optimization.
Structural analysis is solved using the finite element method. Current analysis capabilities include static, normal modes, direct and modal frequency analysis, random response, heat transfer, system buckling calculations, acoustics and Fatigue analysis.
Structural optimization types include sizing, shape, topology, topometry, topography and freeform optimization. Special advanced features include: multi-model optimization (MMO) and reliability based optimization (RBO).
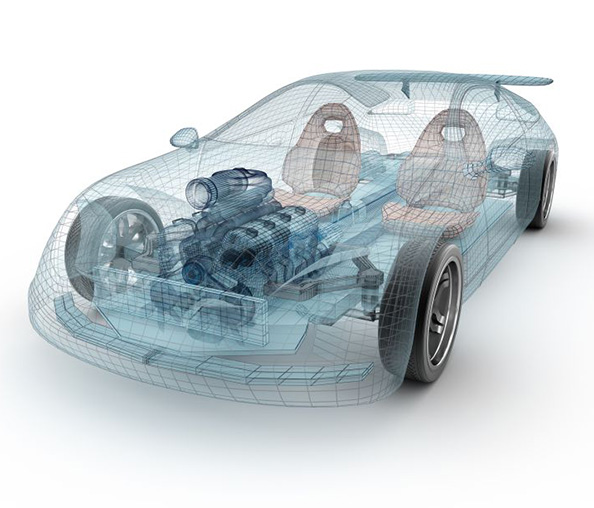
Solutions provided from Genesis®
- Automotive OEM – Light-weighting & cost reduction requirements set by the government CAFÉ standards
- Automotive Tier Suppliers – Support needs for whole CAD/CAE solution
- Engineering Consultants – Provide an environment for innovation and multidisciplinary optimization for coupling almost any 3rd party engineering software
- Aerospace – Improve the design target and satisfy design requirement in efforts to reduce cost and light-weighting
- Heavy Industry – Reducing weight while improving rigidity of machine to result in a more efficient design
Some benefits of Genesis® include:
- Reduction in cost and improvement in performance – By generating new designs based on user criteria such as mass minimization, frequency maximization, stress or displacement constraints and more.
- Reduction in engineering time – Genesis® has powerful embedded solvers such as our SMS eigensolver, which speeds up solving time and are quick for small to midsize problems and even faster for very large problems.
- Innovative designs come to life – Robust designs can be realized as our optimizer BIGDOT, can handle extremely large numbers of design variables. This allows an engineer to explore the entire design space with either topology, topometry or topography optimization.
Special application of Genesis®:
- Additive Manufacturing – One important usage of Genesis® topology optimization is for Additive Manufacturing.
- Genesis® can generate optimal shapes and together with Design Studio, the user can automatically generate lattice structures.
- Genesis® can perform topology optimization with additive overhang angle constraints to build the structures with minimum support material.
- Genesis® can perform sizing or topometry optimization to find the optimal dimension of lattice members.
Genesis® for Ansys Mechanical
Genesis® Structural Optimization Extension for ANSYS® Mechanical
Genesis® Structural Optimization for ANSYS® Mechanical (GSAM) is an integrated extension that adds structural optimization to the ANSYS® environment. GSAM can perform topology optimization as well as topography, freeform, sizing and topometry design.
Genesis® Topology Optimization for ANSYS® Mechanical (GTAM) is a subset of GSAM. GTAM is limited to topology optimization only.
The highlights of GSAM and GTAM include:
- Easily add structural optimization to existing ANSYS® Workbench workflows
- Easy and fast to create structural optimization data
- Easy and fast to post-process structural optimization results
- Export optimized geometry in STL or IGES format
- High-end solution for multiple types of the parameter-free optimization
- Optimize for multiple types of responses including static, modal, harmonic, thermal, random vibration and etc.
- Robust and efficient solver: used and proven by a lot of industrial clients
The benefits of GSAM and GTAM include:
- Tight integration with ANSYS workbench: Allowing the user to set up the structural optimization problem, optimize, post-process, export optimized geometry within ANSYS® environment.
- Guides new designs: Engineers will be led towards the most structurally efficient use of material
Identify and resolve design issues: Quickly identifies areas where designs need to be improved and use - structural optimization to improve the performance in the most efficient way possible
- Reduce development time: Get the design right the first time with less iterations
- Additive Manufacturing: GSAM/GTAM can generate optimal shapes that can be produced using 3D printers.
- Additive overhang constraint helps creating support free structures
ESLDYNA – Large Scale Optimization for LS-DYNA® Analysis
ESLDYNA is based on the Equivalent Static Loads (ESL) method which takes advantage of the ability of Genesis® to solve large scale optimization problems using external responses from the LS-DYNA nonlinear finite element solver. One of the key advantages of ESLDYNA is to significantly reduce the run time by identifying high performance designs with only five to ten nonlinear analyses.
(*) LS-DYNA is a trademark of Livermore Software Technology Corporation. LS-DYNA is a general-purpose finite element program capable of simulating highly nonlinear, transient dynamic problems.
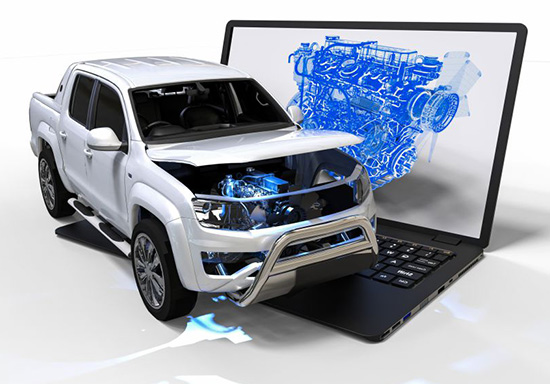
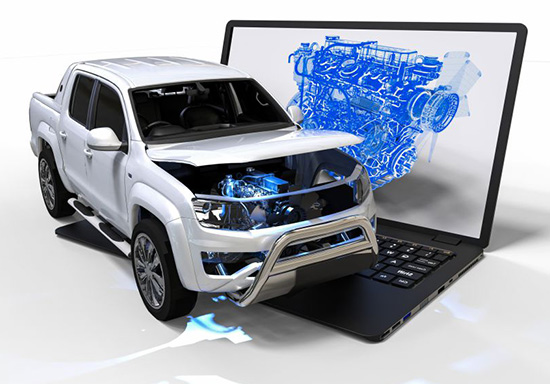
ESLDYNA – Large Scale Optimization for LS-DYNA® Analysis
ESLDYNA is based on the Equivalent Static Loads (ESL) method which takes advantage of the ability of Genesis® to solve large scale optimization problems using external responses from the LS-DYNA nonlinear finite element solver. One of the key advantages of ESLDYNA is to significantly reduce the run time by identifying high performance designs with only five to ten nonlinear analyses.
(*) LS-DYNA is a trademark of Livermore Software Technology Corporation. LS-DYNA is a general-purpose finite element program capable of simulating highly nonlinear, transient dynamic problems.
Benefits
- Reduced Computational Cost. Solution converge in only 5 to 15 design cycles
- Easy implementation of Shape, Sizing, Topology, Topometry, Topography, and Freeform design changes
- Simple and efficient coupling using a Design Studio Plugin
Highlights
- Seamless integrates Genesis® optimization capabilities with LS-DYNA® analysis
- Multiple LS-DYNA® loading conditions or input files can be considered simultaneously
- Linear loading conditions/analysis can also be used in the same optimization. This allows for MDO optimization (e.g. simultaneously optimize for stiffness and NVH)
Ability to transfer data between FE Meshes of different resolutions
Connect with us now for complimentary webinars and evaluation software.
Our engineering team can work with you to conduct a Test Case showing how OmniQuestTM will improve your designs, processes and your overall business.